Keywords: Computational Fluid Dynamics (CFD), Air intakes, Aerodynamic analysis, Velocity Contours
About
The gas turbine is an internal combustion engine that uses air as the working fluid. The engine extracts chemical energy from fuel and converts it to mechanical energy using the gaseous energy of the working fluid (air) to drive the engine and propeller, which in turn propel the airplane. As air passes through a gas turbine engine, aerodynamic and energy requirements demand changes in the air’s velocity and pressure. During compression, a rise in the air pressure is required, but not an increase in its velocity. After compression and combustion have heated the air, an increase in the velocity of gases is necessary in order for the turbine rotors to develop power. The size and shape of the ducts through which the air flows affect these various changes. Where a conversion from velocity to pressure is required, the passages are divergent. Conversely, if a conversion from pressure to velocity is needed, a convergent duct is used. Air Intakes are a necessity for any air-breathing engine, which are incorporated in most aero systems. The efficiency of the air intake directly and greatly influences the engine’s propulsive power This work explores the types of air intakes used in aerospace propulsion, their classification into different categories based on function and design. The types are then investigated through a survey of their application(s). The design – a bellmouth air intake used for ground testing is then studied. Effects of curvatures based on geometry of intakes have been studied using literature surveys of experiments involving CFD computations which employ RANS solver and Navier-Stokes Equations. To develop understanding of the regime of flow in and around a bellmouth air intake, pressure and velocity contours are generated using a commercial CFD program - ANSYS FLUENT, at different mach numbers and a mass flow rate of 11.8kg/sec. The process of air profiling, meshing and analysis is entirely done using ANSYS. Geometry of the bellmouth air intake is initially fabricated using CATIA V5. A grid independence study is carried out and an optimum meshing profile is chosen for the CFD analysis, particularly velocity and pressure contour plotting.
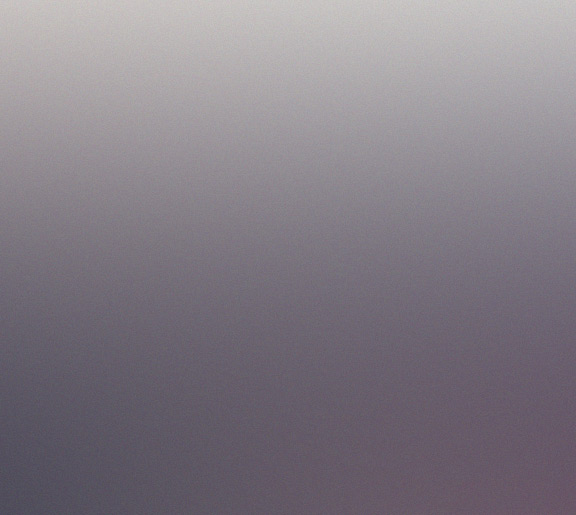
Results
Various types of air intakes with their functions were reviewed and their strengths were identified. The effects of curvature on flow regime were surveyed. The best design for Bellmouth intakes was identified and its construction based on various parameters was discussed. The study was carried out to validate a 3-dimensional Computational Fluid Dynamics (CFD) model of a bellmouth intake with an elliptical design profile with the use of the CFD model as a design tool to replace or reduce the frequency of hydraulic model studies. A model was designed using CATIA V5, meshed and analyzed using ANSYS FLUENT and the results were presented and discussed. This finally paved way for generating conclusions about the behavior of flow in bellmouth air intakes and mapping it with results of simulation. Please note this is a project conducted under the Defense Research Development Organization (DRDO), Ministry of Defense, Government of India. Hence, all figures and specifications related to the project are omitted to maintain confidentiality. However, a general approach to the problem is listed above.