Keywords: Aerodynamics – Separation delay – Active Flow Control: Plasma actuator – Aerodynamic modelling: Computational Fluid Dynamics (CFD)
About
Plasma jet actuator as a method of active flow control has proven to significantly delay stall, improve lift and reduce drag of airfoil while not taking a toll on the weight profile of the airfoil. However, selection of an optimum design of actuator is significant as it directly influences the capacity of the actuator to perform required function. This study furnishes numerical study conducted over a NACA 0015 airfoil, both with and without a plasma jet actuator, to estimate the aerodynamic benefits of a Dielectric Barrier Discharge (DBD) plasma actuator. It gives a thorough Computational Fluid Dynamics (CFD) analysis to estimate the effect of the actuator on the lift, drag and stall angle for a non-cambered airfoil like NACA 0015. The NACA 0015 airfoil is assigned a chord length of 150 mm and a span of 600mm, with the actuator mounted at mid-chord. ANSYS Fluent is used in the simulations. The angle of attack impact is also examined with 0° to 20° attack angles. The plasma is introduced using a user- defined function and the effect with related conclusions are elucidated with the help of streamline plots. This work also outlines the drawbacks and benefits of the solution approach.
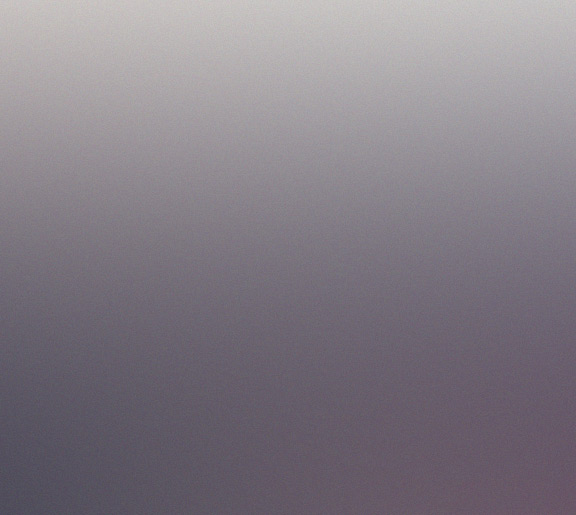
Results
This work provides a robust numerical study that shows the delay of stall angle for a NACA 0015 airfoil by employment of a DBD plasma actuator. The actuator thus, serves the purpose of delaying stall by 3 degrees when assembled at 50% chord length. The streamline plots help visualize this delay effectively. Overall, this study also facilitates a unique solution for geometric distortions caused by the actuator by modelling one of the thinnest known plasma actuators (as of June 2020). This actuator has also been tested experimentally on a flat plate by the study team and the design effectively sustains high voltages (DC and AC, maximum voltage for DC setting was 4.5 kV and for AC setting was 7.7kV), and the material adhesive fulfils its purpose throughout the duration of testing – which implies more experimental research into the design presented could be rewarding. For more information on the numerical study, refer to the associated publication: Mukesh, M & Javaria, Gunjan & Mahawar, Vaibhav & Rawat, Pratishtha & Kumar, Hemantha. (2020). “CFD Analysis to Study Flow Separation Control Using a Plasma Jet Actuator for Non-Cambered Airfoil”. GIS-SCIENCE Journal, VOLUME 7, ISSUE 8, SEPTEMBER 2020. ISSN NO. : 1869-9391. The experimental study report can also be requested at pratishtharawat.ae16@rvce.edu.in